Some may be persuaded that as the Netherlands is a small country it only could produce a proportionally small defence sector. Not so, the Netherlands offers a wide variety of trade opportunities in the defence sector. One of them lies in the F-16 MLU replacement program. The setting, on 22 April 2004, couldn’t be more appropriate. Namely, in a windy and inclement Noordoostpolder (the Netherlands) the German-Dutch Wind Tunnels (DNW) offered the press an unique insight of its latest prize acquisitions. The focus of the day was their contributions to the development of the, by Lockheed Martin Aeronautics Company (LMAC) led, F-35 Joint Strike Fighter (JSF) program.
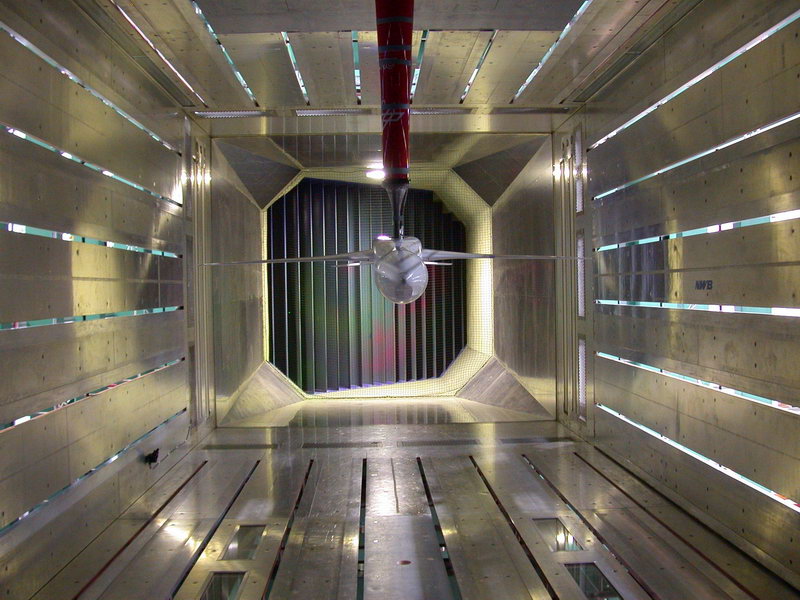
DNW, a non-profit organisation under Dutch law, is an organization dedicated to aeronautical testing excellence and provides a wide spectrum of wind tunnel test and simulation capabilities. DNW was established by two national laboratories, the National Aerospace Laboratory of the Netherlands (NLR) and the German Aerospace Centre of Germany (DLR). Today, in addition to the Engine Calibration Facility (ECF) as well as the jointly developed Large Low-speed Facility (LLF), the largest low-speed wind tunnel in Europe, both in the Noordoostpolder, DNW operates all major aeronautical wind tunnels of NLR and DLR. These are grouped in three business units: ‘Noordoostpolder’ (NOP) and ‘Amsterdam’ (ASD) in the Netherlands and ‘Göttingen und Köln’ (GUK) in Germany.
LMAC selected DNW-LLF, in an internationally competitive field, as one of only a few test sites for the inlet compatibility test. “The projects at NOP facilities consists of two extensive test campaigns regarding the Inlet Distortion and Short Take-Off and Vertical Landing (STOVL) performance,” said Hans van Ditshuizen, Business Development DNW. Both tests are performed in the framework of the System Development and Demonstration (SDD) phase under contract by LMAC.” With this latest acquisition DNW has been recognized by LMAC for its unique features for aircraft modelling testing. “Already in the earlier F-35/JSF Concept Demonstration Phase (CDP), the DNW-LLF facility was successfully used for STOVL testing on a scale model, including tests in the Preferred Weapons System Configuration,” tells Joost Kooi, Manager Business Unit ASD. “This contract in 1999 was the first result of the Netherlands attempting to position its national industries and institutes for the F-16 replacement.”
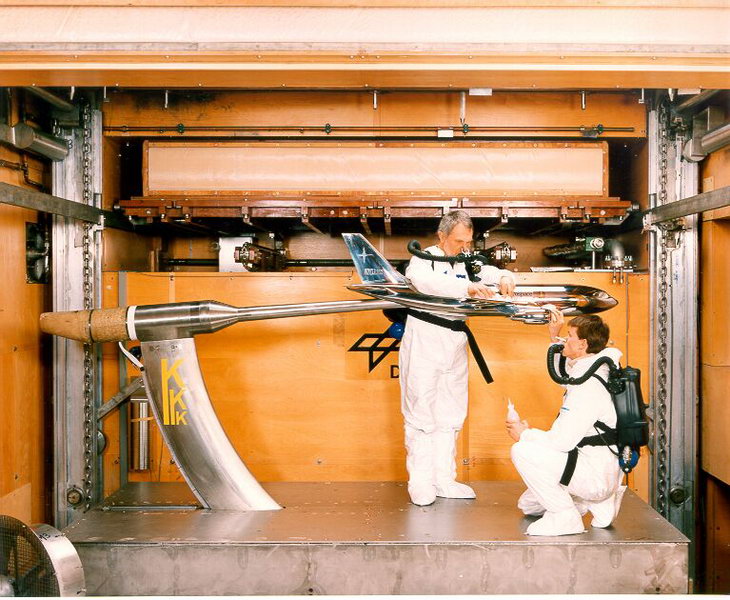
As a direct result of that, DNW-LLF has seen already a number of entries of the F-35/JSF STOVL configuration. “This wind tunnel is capable of providing a combination of specific test conditions needed for the STOVL configuration,” continues Van Ditshuizen: “a nearly constant flow at very low speeds (down to 15 knots) and a large amount of compressed air to simulate jet exhaust effects on lift fan, core engine and roll nozzles of the aircraft. In actual STOVL operation, power is transferred from the face of the main engine to a rotating main drive shaft. The shaft enters a clutch and, when engaged, the clutch couples the main shaft to the lift-fan engine. The lift-fan itself has no self-contained power source, but is capable of turning the 29,000 hp. delivered by the shaft into about 20,000 lb. of thrust. Air enters the lift-fan through a door behind the aircraft’s canopy. Air exiting the lift-fan passes through a variable area vanebox, which vectors the air-stream and also controls the operation of the lift-fan by varying the nozzle exit area. The vanebox is on the underside of the aircraft. To help balance the F-35B in STOVL flight, roll posts with variable area nozzles are located in its wings. The roll posts are fed by the main engine and direct approx. 3,800 lb. of thrust. Also fitted to the main engine is a thrust-vectoring three bearing swivel module (3BSM), which helps direct main engine exhaust down, or parallel to, the aircraft. STOVL inlet testing on the JSF model by DNW-LLF is performed for the full operational envelope of the aircraft (i.e. for forward, side and backward wind speeds) during take-off at very close range to the ground. The LLF large tunnel test section of 9.5 m x 9.5 m is selected for the majority of the tests to avoid interference from the recirculation of jet exhausts with the flow around the model. Another advantage of the large test section is that the models can be tested down to very low speeds (15 kts). A ground plane with scoop is used as a boundary layer control device. The ground plane is a 6.3 m wide and 7.6 m long conveyer-type belt and it replaced the standard test section floor. When installed, the upper surface of the ground plane was 0.2 metres higher than the test section floor. This distance is needed to allow the scoop installed at the leading edge of the ground plane to remove the oncoming tunnel floor boundary layer that forms upstream of the test section. Alraedy, it was clearly demonstrated that the LLF is capable of providing the unique combination of specific test conditions needed in the STOVL configuration – a nearly constant flow at very low speeds (down to 15 ± 0.5 knots), very accurate model height positioning via the LLF sting mechanism (± 2.5 mm from the set-point), an accurately known but large amount of compressed air and a large tunnel section with negligible wind tunnel wall/floor effects providing LMAC with high quality data at even higher productivity. During the inlet distortion tests, large amounts of compressed air (maximum 15kg/s) flow through the lift-fan (around 8kg/s) and through the main engine inlets (around 7kg/s). These measurements, conducted at speeds of up to 125kts, take place in the 8 x 6m or 6 x 6m cross-section area instead of the 9.5 x 9.5m area.”
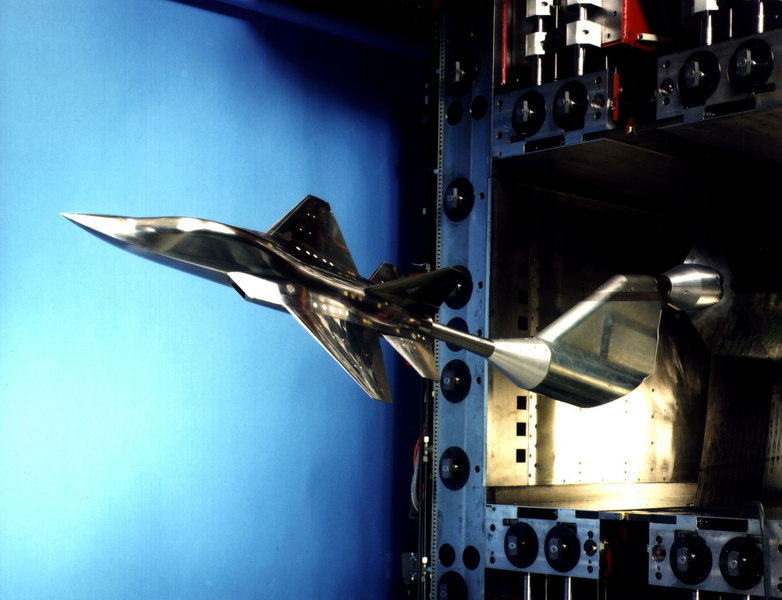
Pratt & Whitney (P&W) began testing the first, SDD Block 1, STOVL propulsion system and its lift system for the F-35/JSF on 14 April 2004. “The hardware being evaluated at the P&W company’s West Palm Beach, Florida USA, facility,” said Ivor Evans, F-35/JSF International Program Manager, LMAC, United Kingdom, “represents the F-35B entire propulsion package, including the F135 main engine as well as a Rolls-Royce lift-fan, clutch, main drive shaft, lift-fan gearbox, variable area vanebox nozzle, 3BSM and wing-mounted roll posts. Tests already conducted with the propulsion system examined performance and operability under conventional flight conditions and under STOVL flight conditions at idle speeds are successfully. They also run the propulsion system up to the thrust levels required for F-35 hover, and to conduct the systems first dynamic clutch engagement. In the latter, the main engine is run up to speed, the clutch is engaged, and the drive shaft coming off the F135 supplies power to the lift-fan. An important thing about these tests is the data collected on the low-pressure turbine, which is the key to running the lift-fan, because the shaft that drives the lift-fan is powered by it. Rolls-Royce plans to deliver two additional lift systems to P&W by July 2004. It has been well publicized that we have been wrestling with a weight issue on the F-35B version, the most complicated version of the three aircraft developed. At the same time, there are, however, no weight requirements but there are instead performance requirements. On the other hand, we are at this point only a quarter into a ten-year development program. Not to state the obvious, but this is one of the purposes of the SDD phase–to boil out issues like weight.”
All Block 1 hardware, does not have the entire spectrum of weight-saving features to be included in subsequent initial flight release (IFR) hardware. Although, it is lighter than the equipment used in the JSF CDP. Approximately 790 lb. were taken out of the lift system, with more than 600 lb. coming out of the lift-fan itself. Also Block 1 systems have more functionality than those used in the JSF CDP, and they were designed with full aircraft operational life in sight. Had the STOVL systems clutch a limit of 100 engagements during the CDP. For SDD, the clutch has already performed the operational minimum of 1,500 engagements. Differences between Block 1 systems and IFR hardware will be, for the most part, oriented toward weight reduction. The first IFR lift system is expected to be delivered to P&W mid next year.
“This contract for DNW is another step for Dutch participation in the JSF program, but certainly not the end of the road,” said Rini Goos, Commissioner for Military Production, Netherlands Ministry of Economic Affairs. “As a Level 2 partner we have great confidence in the system and the program. Today’s contracts are a clear indication of the strength gained by the Dutch governments joint efforts with its industrial base, and they also demonstrate the effectiveness of that partnership on the international defence scene. The programme still provide great opportunities for our highly competitive and extremely capable industries, both for the transfer of technology knowledge as well as for production. We look forward to further Dutch industrial participation as the program progresses.”
The participation of the Dutch aerospace industry could reach approximately 5% of each aircraft built (expected totals are more likely to be in the 4,000-5,000 aircraft range up to 2028 than the 6,000+ sometimes cited). This is in contrast to the former compensation orders, in which the volume of work awarded to a specific country was only in proportion to the number of aircraft ordered. The Dutch JSF business currently exceeds $220 million in the country’s work share in the F-35/JSF program.
“Even though the F-35/JSF programme lies under attack over cost, technology transfer and work share,” said Major-General Peter Vorderman, Chief Materiel RNLAF, “and despite some resistance in the ranks of Dutch parliament and the media. This aircraft still is the best candidate, both on price and performance, to replace the RNLAF 108 F-16’s MLU. The Dutch investment of US $800 million in the SDD effort is raised partly by the defence and economic affairs ministries, and partly by industry. From the start of the production phase, the latter will pay a levy of 3.5% on the value of JSF orders back to the state. F-35/JSF production totals are likely to be in the 4,000-5,000 aircraft range. The benefits of this will to a large extent accrue to the government, in particular the Ministry of Defence.”
Although, investing in this largest ever DoD acquisition program is not actually a formal commitment to purchase the F-35/JSF, it is in effect a de facto decision to purchase some 85 of the type to replace RNLAF F-16s in the 2010 to 2025 timeframe. A budget allocation of 5.5 billion euros has been set aside to fund this procurement. The Netherlands has been part of the JSF program since 1997. But beyond the politics and bureaucracy related to the aircraft’s technology, there is still the issue of when the F-35 will be ready to fly and at what price?
“Nevertheless,” conclude Van Ditshuizen, “DNW can look back on a number of positive developments in terms of test volume in the SDD phase of the F-35/JSF development. DNW is proud of having gained this contract through hard work and look for a lot more to come.”
Leave a Reply